Published on 07 September 2021
STEP 5 & 6
- date07/09/2021
- lieuLimoges
INDUSTRIALIZATION & PRODUCTION
Once a new TEXELIS prototype has been developed, validated and tested, the final stage is production. Before this can begin, the new product must be industrialised – a critical step that includes defining the production process and tailoring our manufacturing capacity to match customer requirements. Then production can begin!
PRODUCTION VOLUMES
The Texelis facility in Limoges is equipped to handle small production volume as well as large production volumes that run over several years. Thanks to a flexible production force, we can adapt delivery cadence in line with customer requirements. Our production values ensure the highest quality certifications, market-leading terms and conditions, and delivery timelines designed to suit customer intake capacity.
In early 2021 Texelis received the first order from the DGA for 364 Serval vehicles. The first vehicles will be delivered in early 2022, with more to follow by the end of the year. This production run includes 1200 parts to be machined or assembled, and a supply chain that includes 800 suppliers. By 2031 nearly 1,000 vehicles are expected to have been ordered and manufactured in our dedicated, 2700 sqm Serval production area.
MOBILITY KITS
Texelis’ mobility kits for monohull vehicles allow our customers to order our range of rolling chassis products as a tailor made solution. These technically mature, de-risked designs have been assembled and tested on multiple vehicle. The result for our customers is guaranteed reliability, proven and fully-qualified equipment, and reduced development times and costs.
Each modular mobility kit is available in a number of different versions, giving customers the flexibility to select the option that best suits their requirements. Each kit includes powertrain, transfer case, transmission and steering system.
INTEGRATED LOGISTICS
Texelis’ Product Lifecycle Management (PLM) tool is a collaborative tool that allows us to centrally integrate all product data on a single platform. We have taken this approach as it allows us to demonstrate improved configuration management with an Integrated Logistic System.
We initiated the PLM for the Serval programme in order to increase our industrial performance, enhance our commercial competitiveness, strengthen traceability, and improve life-cycle management for delivered equipment.
CUSTOMER SUPPORT
Throughout industrialisation and production, the customer remains at the centre of the process with Texelis. Supported by our design, engineering and testing personnel, each Texelis project is led by a dedicated technical support team that works to provide the best delivery terms, quality and cost-efficiency throughout production, assembly, testing and delivery.
We have built our business on transparency for our customers. Texelis products are licence-free and defined by clear and understandable export policies. Our accessible facilities operate an ‘open door’ policy, and we welcome our customers to our site in Limoges to discuss new or ongoing projects at all times.
KNOW-HOW & EXPERIENCE
Texelis takes a dedicated approach to the transmission of skills within our business, with our Turning Know-how into Experience (TSE) programme. This allows us to effectively preserve knowledge and understanding, promote skills development and diversity, and conserve expertise over the long term. .
Texelis launches ten TSEs each year, and more than 100 Texelis employees have benefitted from the TSE programme since 2012. Not only does this result in a more engaged and efficient workforce, it centralises skills development management within our organisation for the benefit of our customers and partners.
Latest news
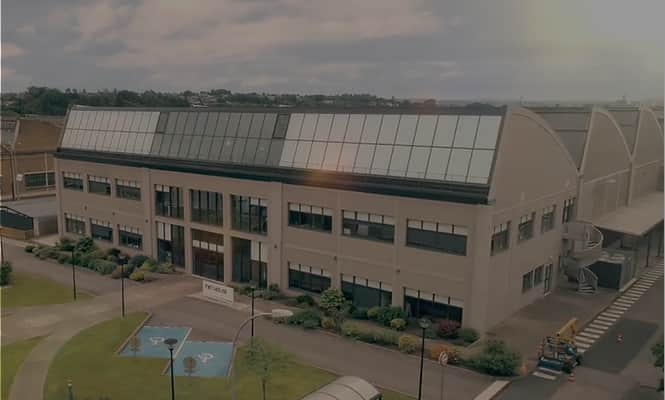
Contact
Send email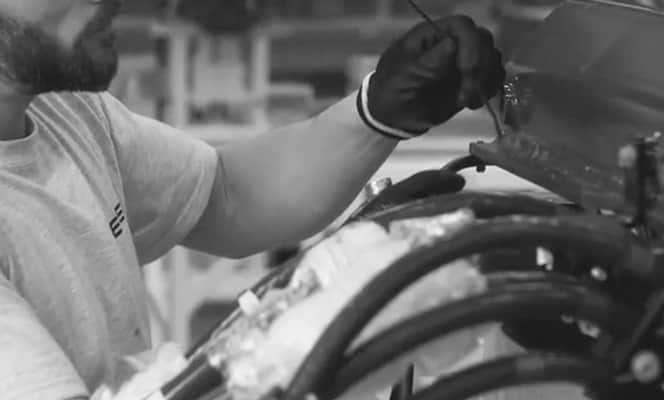